自動車の構造
モノコックボディ構造
現在の乗用車の構造は「モノコックボディ」が主流になっています。特に国産乗用車のセダンタイプにおいては、全てがモノコックボディを採用しています。モノコック構造とは、「飛行機」や「トンネル」に代表されるような「衝撃を外皮全体で吸収する構造」のことで「応力外皮構造」とも言えます。自動車の場合には、視界確保や乗降のための広い開口部が必要なため、メンバーやピラーを組み付けており、純粋なモノコック構造とは言えませんが、受けた衝撃を外皮全体で吸収するという性格はモノコック構造と変わりません。
自動車のボディは、薄い鋼板をプレス加工した様々な形状の部品を、溶接によって組合わせ作られています。鋼板の加工には様々な種類がありますが、代表的なものが「フランジング」と呼ばれる、鋼板を直角に曲げる加工方法です。鉄には曲げると曲げた部分の結晶にひずみが生じ、曲げた部分の硬度が増す性質があります。この性質を「加工硬化」と呼んでおり、自動車のボディに有効的に利用されています。また、部品の組付けには、スポット溶接と呼ばれる溶接方法が用いられ、溶接個所は7000点にも及びます。
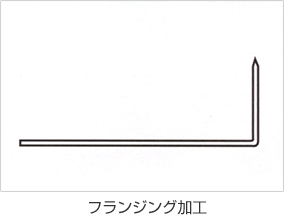
モノコックボディの特徴として、大きな力が加わった際に、衝撃エネルギーを様々な方向へ逃がすと同時に、そのエネルギーが奥へ奥へと伝わっていくことがあげられます。この特徴は、安全面では優れているのですが、車体修理や検査面においては、「衝撃エネルギーがどこまで伝わったかを特定することが難しいために、衝撃の出るポイントを絞り込むことが困難になる。」 ということを覚えておく必要があります。
モノコックボディ構造の特徴
<長所>
- 剛性が高い。
- 薄い鋼板の組みわせにより、生産性がよい。
- 車両重量を軽減することができる。
- 衝撃エネルギー吸収効率がよい。
<短所>
- 騒音、振動の影響を受けやすい。
- 衝突時の損傷形態が複雑で、復元修理が困難である。
フレーム構造
フレーム構造の自動車に使用されるフレームは、数種類あり、乗用車に使用されるものは「ペリメータフレーム」、トラック等では「ラダーフレーム」と呼ばれるものが一般的に使用されています。
フレーム車は、エンジン、懸架装置、操舵装置等をボディとは分離したフレームに取り付け、ゴムのブッシュを介してボディを組み付けています。このためフレームには走行中に起こる振動、ねじり、曲げ等の影響を受けるために剛性の高いものが要求されます。
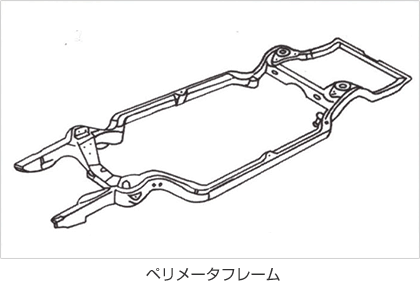
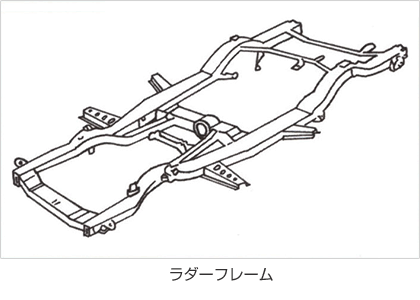
フレーム構造の特徴
<長所>
- 路面やエンジンからの振動を室内に伝えにくい。
- 衝突エネルギーをフレームに集中させることにより、客室への衝撃エネルギーを軽減させることができる。
<短所>
- フレームを作るための高度な技術が必要とされる。
- 車両重量が増し客室が高い位置になる。
以上、モノコック構造とフレーム構造を比較すると、それぞれにメリット、デメリットがあります。これらを時代の背景に照らし、生産性や省エネルギーといった観点から考えた結果、大量生産に向き、車両重量が軽いモノコックボディが脚光を浴びるようになったのです。
自動車の走るための基本設計は「走る」「曲がる」「止まる」の3つの原則から設計されています。特に事故等で大きな衝撃を受けた際に、第一段階として「走る」ことに関連する懸架装置の取り付け部が狂うことがないように衝撃吸収部位を設け、第二段階としては乗員の安全を確保するため、客室が壊れないようにフロント部及びリア部に衝撃吸収部位を設けてあります。
この衝撃吸収部位は鋼板に「穴」を開けたり、各メンバー等の形状に急変部を持たせることにより、衝撃を吸収させていることを覚えておく必要があります。
自動車の各部名称
各自動車メーカーにより、各部名称の呼称は異なっておりますが、「ガリバー」「ドルフィネット」においては下記のように統一します。
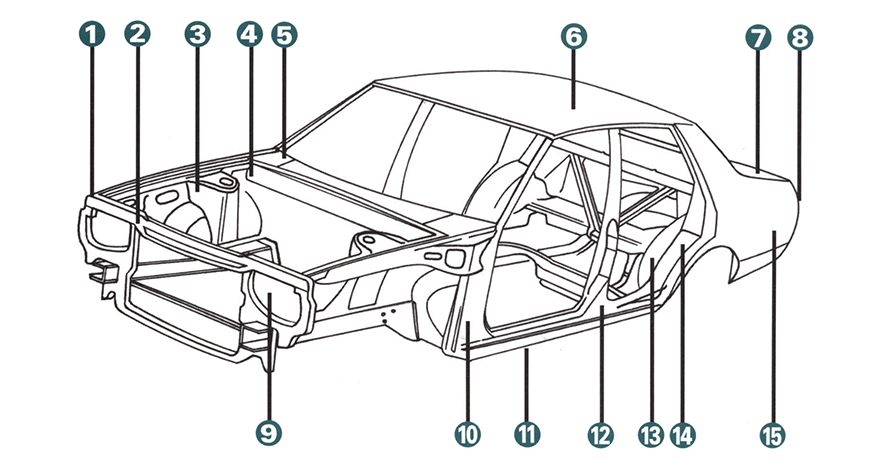
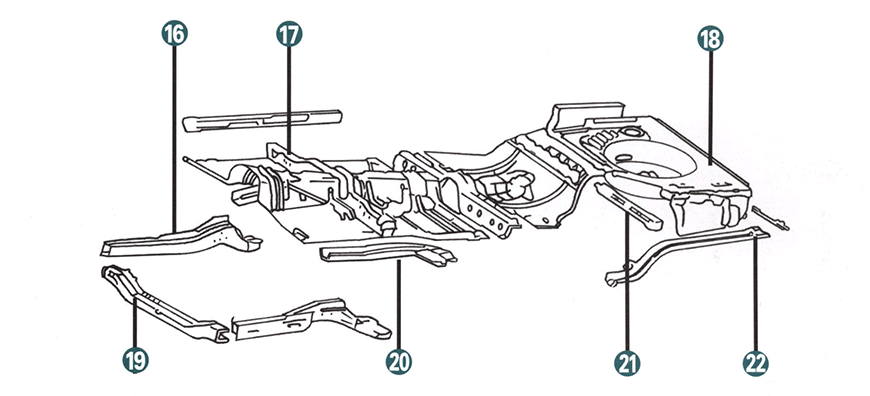
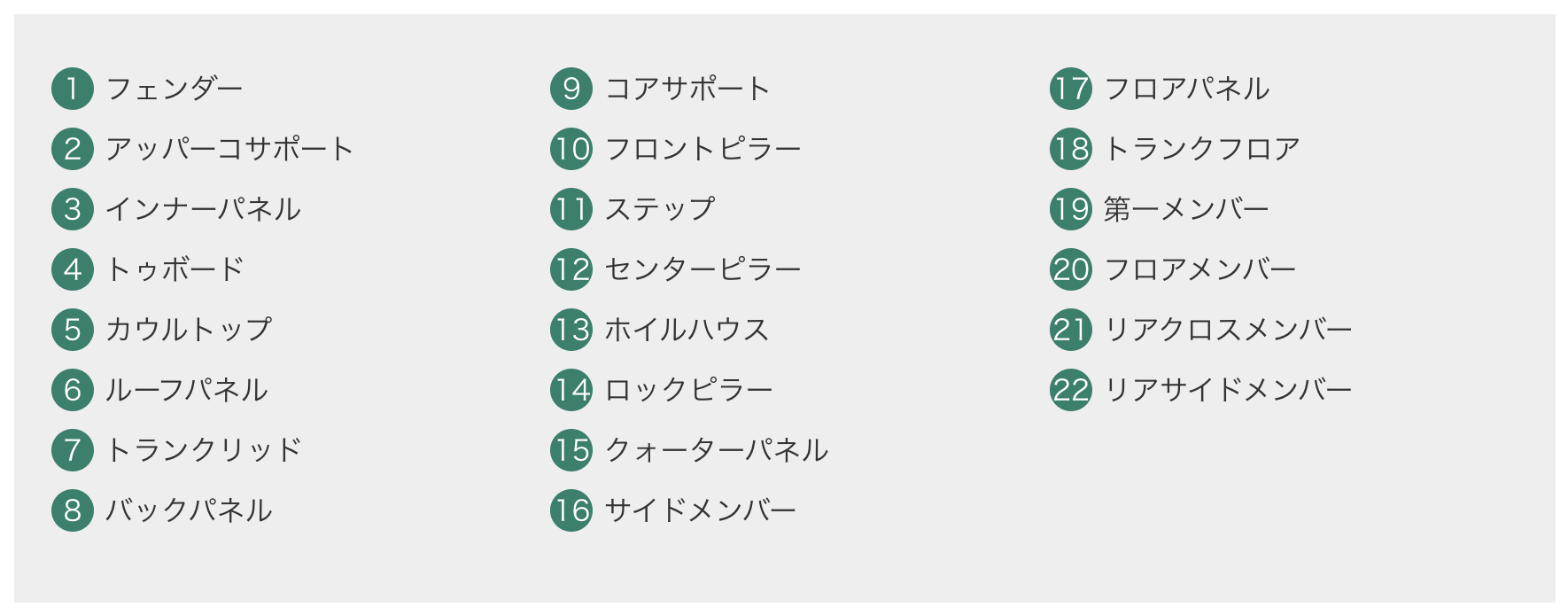
中古車査定・中古車販売の関連ページ

事故車は買取価格が安くなる。そもそも買い取ってもらえない。そんな話を聞いて、自分が乗っているクルマは事故車になるのだろうかと気になる方もいるのではないでしょうか。査定士の判断基準を解説します。
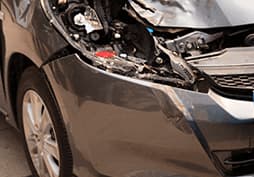
クルマ選びは「修復歴」も必ずチェックしましょう。修復歴のあるクルマは走行機能に影響がある場合もあります。ガリバーでは、入庫時に徹底的な検査を行っているので、お気軽に店舗スタッフにおたずねください。
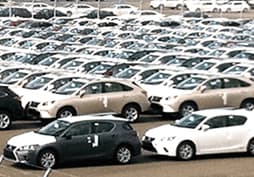
事故車は買取価格が安くなる。そもそも買い取ってもらえない。そんな話を聞いて、自分が乗っているクルマは事故車になるのだろうかと気になる方もいるのではないでしょうか。査定士の判断基準を解説します。